XCMG HOWO トラック用の円筒形ギア トラックのスペアパーツを駆動
駆動用円筒歯車
スペアパーツは多数の種類があるため、Web サイトにすべてを掲載することはできません。具体的なものについてはお気軽にお問い合わせください。
アドバンテージ
1. 当社はオリジナル製品とアフターマーケット製品の両方を提供します
2. メーカーから顧客へ直接届けるため、コストを節約できます。
3. 通常部品の安定在庫
4.納期通りに、競争力のある配送コストで
5.プロフェッショナルで時間通りのアフターサービス
パッキング
カートンボックス、またはクライアントの要求に応じて。
説明
補助ボックス駆動歯車部品の厚肉と薄肉の特性により、対応する鍛造金型のキャビティも比較的深く、キャビティ壁は薄くなっています。成形プロセス中に、金型の薄壁にクラックが発生しやすく、金型の寿命が低下します。鍛造品のコストは依然として高い。
独自技術の副箱ドライブギヤ
図1 某補機箱のドライブギヤ
補機駆動歯車部品の型鍛造方法は、通常、自由鍛造が最も多く使用されています。この方法の利点は、ダイ壁の厚さにあります。金型の力は金型の寿命を確保するための緩衝材の役割を果たしますが、バリの材料損失は鍛造品重量の10%~50%、平均で約30%であり、材料コストが大きく影響します。型鍛造品はコストの60%~70%がかかるため、この種の鍛造品をクローズド生産に変更しました。
原因分析
密閉型鍛造とは、ブランクを据え込みまたは押し出しによって閉じた溝の中で鍛造品に変形させることです。密閉型鍛造は、開放型鍛造と比較して、最終成形品を型壁でブランクで充填する必要があるため、より高い型壁強度が必要となります。従来の設計では鍛造品のキャビティのみを考慮しており、金型壁の強度は十分に考慮されていませんでした。ただし、図2の赤で示した部分は埋める必要があります。ブランクが外壁に接触した後も金型を押し続ける必要があるため、金型と鍛造金型の壁に過剰な力がかかります。弱点、特に根元フィレット(図 3)は、成形後期に過度の力がかかると破損します。
改良型密閉熱間鍛造プロセス
このような薄肉フランジ鍛造品では、金型の寿命を向上させるために、金型構造の変更、金型全体の本体構造への変更、金型設計思想の調整などを統一的に検討してきました。 φ89.6mmの金型に過度な力がかからないよう、充填しにくいφ66.5mmの部分を別構造とすると同時に、φ89.6mmにベントホールを増やして成形時の息苦しさを軽減しました。図 4 に示すように、プロセスが実行されます。変更後は金型寿命が従来の1500個から約3000個と大幅に向上しましたが、依然として現場生産のニーズ、特に自動ライン生産の金型寿命ニーズには応えられません。
鍛造全体を再解析し、鍛造工程で使用する材料を変更しないことを前提に、前鍛造金型と最終鍛造金型の設計において、まず金型寿命の確保の2点を保証します。ひび割れすることなく設計要件を満たします。第二に、鍛造です。金型の取り出しはスムーズで、詰まり現象はありません。鍛造品の上型の側壁の厚みは薄く、鍛造品の成形過程において上型にかかる衝撃力は下型に比べてはるかに大きいと考えられます。そのため、鍛造品は折り返すように設計されており、金型の肉厚部分は上型に設計されています。薄肉部は下型内で設計されており、下型の薄肉部と成形外輪は図5の43型外輪のように全体として設計されています。設計プロセスにおいて、鍛造前の設計は最も重要であり、設計者の技術レベルを最もよく反映できます。予備鍛造は主に材料の分離の役割を果たし、最終的な鍛造成形の準備を行うことができます。設計では、鍛造品の後方押し出しを可能な限り減らし、成形力を低減するために、ブランクリフローを行わずに、予備鍛造品を可能な限り厚くし、最終鍛造溝のキャビティを埋めるように設計しています。鍛造品の折れ曲がりを軽減します。結果として生じるリスク。
新しいアイデアに従って金型設計が実行された後、鍛造品は完全に鍛造され、金型寿命は設計要件に達します。この金型をマルチステーションまたは高エネルギースクリュープレスで使用すると、金型の寿命が元の製品の 2 倍以上に延び、それによって鍛造コストが削減され、労働者の労働力が軽減されます。
結論は
この記事では、補助ボックス駆動ギア部品のさまざまな金型設計プロセスを比較して、次の結論を導き出します。
鍛造前キャビティを設計する際には、鍛造成形プロセス中の素材の分布とブランクの流動モードを考慮する必要があります。
このタイプの高翼ドライブ ギアのクローズド プロセスは、特に高速自動ラインでは、他のギアのクローズド プロセスとは異なります。ウォーキングビームは送信速度が比較的速く、人力による干渉を受けにくいため、設計時にそれぞれを十分に考慮する必要があります。作業ステップの位置決めと材料の配分は正確である必要があり、特に鍛造前のキャビティの設計は最終的な鍛造成形に備えて準備する必要があります。
ほとんどの高エネルギープレスでは、通常、据え込み加工と最終鍛造ステップのみがあり、金型の設計はより困難です。好ましい最終鍛造キャビティ設計により、鍛造品のスクラップ率を低減できると同時に、製品構造に起因する金型の壁が薄く割れやすいという欠点を回避でき、それによって鍛造コストを効果的に削減できます。
補助ボックス駆動ギア部品の金型設計は、同様の構造を持つ他の金型設計の参照および参考の意味を持ちます。
私たちの倉庫1
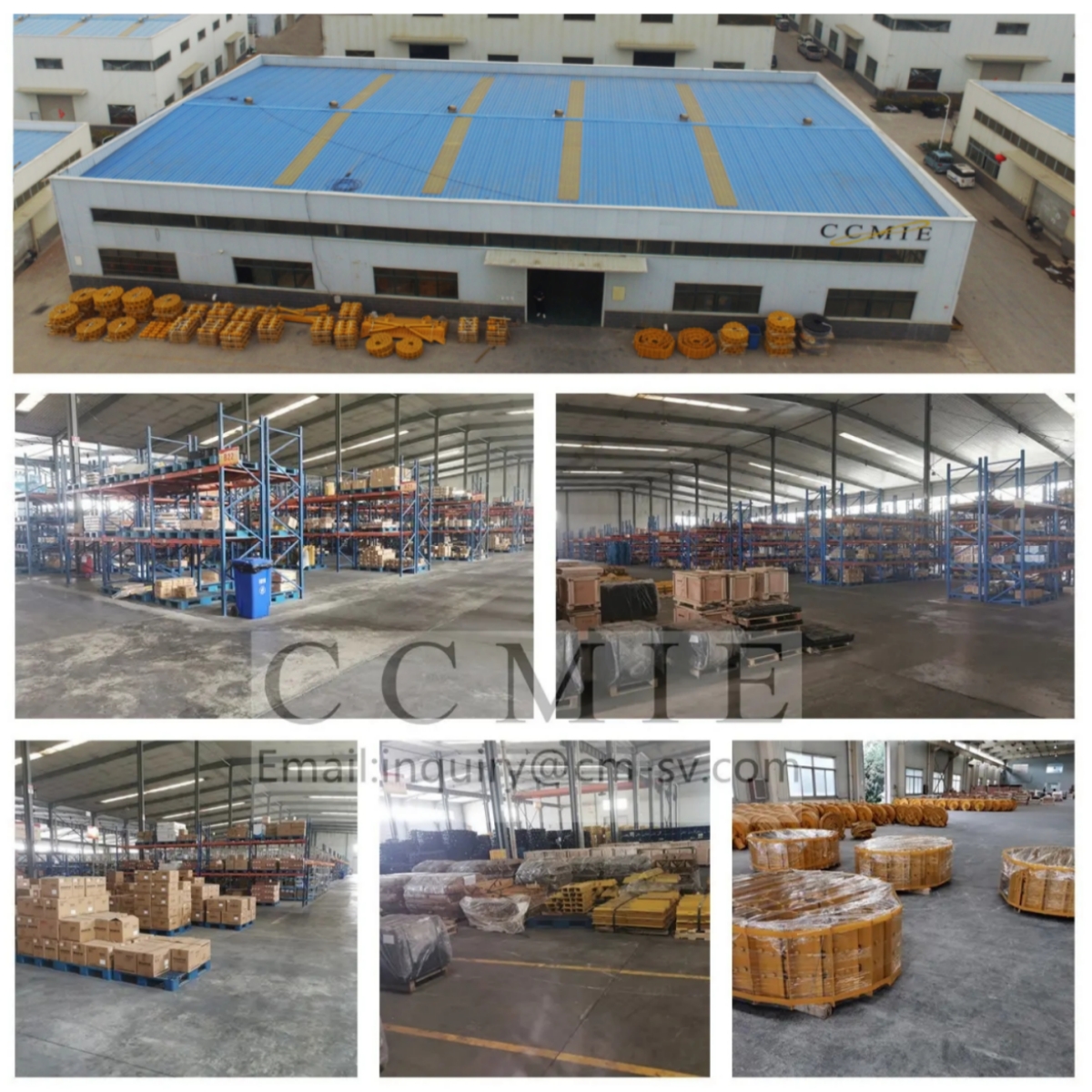
梱包して発送

- 空中ブームリフト
- 中国のダンプ トラック
- コールドリサイクラー
- コーンクラッシャーライナー
- コンテナサイドリフター
- ダディ ブルドーザー パート
- フォークリフトスイーパーアタッチメント
- Hbxg ブルドーザーの部品
- Howo エンジン部品
- ヒュンダイ掘削機の油圧ポンプ
- コマツ ブルドーザー部品
- コマツ掘削機ギヤシャフト
- コマツ PC300-7 掘削機油圧ポンプ
- 六公ブルドーザーの部品
- Sany コンクリートポンプのスペアパーツ
- Sany 掘削機のスペアパーツ
- シャックマン エンジン部品
- Shantui ブルドーザー クラッチ シャフト
- Shantui ブルドーザー接続シャフト ピン
- Shantui ブルドーザー制御フレキシブル シャフト
- Shantui ブルドーザー フレキシブル シャフト
- Shantui ブルドーザー リフティング シリンダー修理キット
- Shantui ブルドーザーの部品
- Shantui ブルドーザー リール シャフト
- Shantui ブルドーザー リバース ギア シャフト
- Shantui ブルドーザーのスペアパーツ
- Shantui ブルドーザー ウインチ ドライブ シャフト
- シャントゥイ ドーザー ボルト
- Shantui ドーザー フロントアイドラー
- Shantui ドーザー チルト シリンダー修理キット
- Shantui SD16 かさ歯車
- Shantui SD16 ブレーキ ライニング
- Shantui SD16 ドア アセンブリ
- Shantui SD16 O リング
- Shantui SD16 トラック ローラー
- Shantui SD22 ベアリング スリーブ
- シャントゥイ SD22 フリクションディスク
- Shantui SD32 トラック ローラー
- 中国汽車のエンジン部品
- レッカー車
- Xcmg ブルドーザーの部品
- Xcmg ブルドーザーのスペアパーツ
- Xcmg 油圧ロック
- Xcmg送信
- 玉柴エンジン部品